Case Studies
The Benefits of a Pleated Filter Boot Re-Design
Challenge:
Pigment plant with air-to-cloth issues in an undersized dust collector. Dust collector is a top entry and top loading style collector using 10ft bags and cages. Temperature is less than 200ºF and operates with a low moisture content in the gas stream. Due to the high air-to-cloth ratio the filter bags had to be replaced every 4-6 weeks.
Solution:
The tubesheet separating the clean air plenum from the dirty side of the collector has a “grid” style bracing system crossing on every second punched hole. This bracing was close enough to the edge of each tubesheet hole that there was very little clearance between the filter bags installed and the edge of this bracing making traditional pleated filters a problem.
Menardi solved this problem by helping to design a new top boot mold that would essentially “notch” out the edges of that boot thereby allowing for install. In these pictures you can see where the edges appear trimmed to allow for install near flat bar.
Results:
By being able to use pleated filters in place of bags and cages the customer was able to drop their air-to-cloth ratio from a moderately high ratio to moderately low ratio. This produced a lower overall differential pressure across the dust collector. Filters now run in excess of 7-8 months before needing to be replaced allowing for much more consistent and longer run times for the customer.
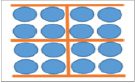
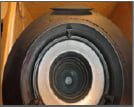
Inside view, looking down pleated filter
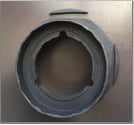
Modification of boot