Case Study
Seam Tape
Challenge:
Customer using a pulse jet dust collector in a mining application-Kaolin. Dust collector was an addition to an existing production line for this customer, but dust collector was all new: ductwork, hoods, housing, filter bags, cages etc. Customer’s process introduced a significantly larger amount of fine particulate matter (less than 2.5 micron) thru the baghouse as compared to most of the other collectors in service. Customer used three sets of filter bags in a 3 month span upon start-up of the new equipment, before getting Menardi involved. Bags were failing due to high differential pressure on the baghouse and by-pass emissions.
Solution:
After reviewing the baghouse operational data and reviewing several “failed” bags from two different suppliers we began to understand the failure method of the filter bags and the baghouse. Part of our solution was to add a seam tape technology to the sewn seams of the filters. Seam tape provides an impermeable barrier over the needle holes that are made during the manufacturing of filter bags.
Results:
Menardi’s filter bags upgraded with the seam tape technology were still in service after six months. Bags were tested for emission bypass using a scanning electron microscope and showed no bypass. Expectations are to get over 1 years lifecycle on filter bags, thereby minimizing downtime and maximizing production.
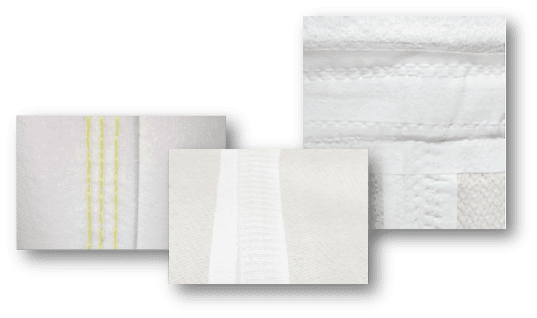